Plastic extrusion for bulk custom plastic parts
Plastic extrusion for bulk custom plastic parts
Blog Article
Secret Benefits and Considerations of Implementing Plastic Extrusion in Your Projects
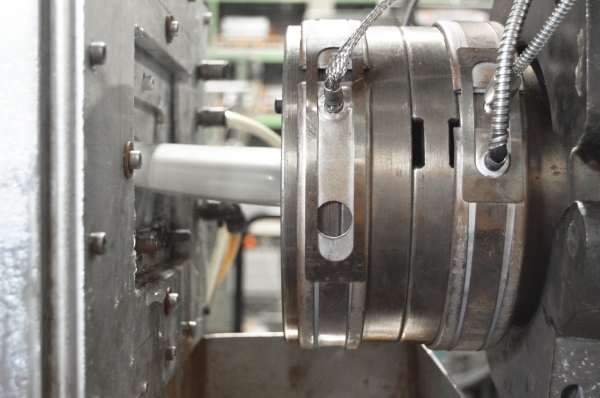
Recognizing the Basics of Plastic Extrusion
Plastic extrusion, a staple in the manufacturing market, is a process that entails melting raw plastic material and improving it into a constant account. The beauty of plastic extrusion exists in its flexibility. The choice of plastic and the style of the die identify the item's features.
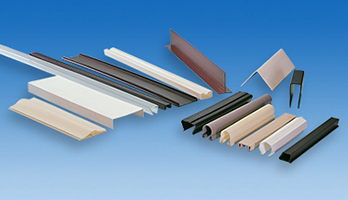
The Economic Benefit of Plastic Extrusion
The financial advantage of plastic extrusion lies primarily in 2 locations: economical product manufacturing and useful manufacturing rates. With plastic extrusion, organizations can create high quantities of product at a reduced cost contrasted to various other techniques. The procedure flaunts an outstanding manufacturing speed, dramatically decreasing time and more improving its economic practicality.
Economical Product Production
A considerable advantage of plastic extrusion is its amazing cost-effectiveness. This production process permits for continuous, high-volume manufacturing with marginal waste, which equates right into lower costs. The raw products made use of, commonly plastic pellets, are relatively low-cost contrasted to other substances (plastic extrusion). The procedure itself needs less energy than several various other production approaches, further lowering prices. Additionally, the extrusion process enables a high level of precision fit the plastic, minimizing the need for expensive post-production modifications or adjustments. The longevity and durability of extruded plastic products commonly mean less require for replacements, contributing to long-term savings. All these aspects make plastic extrusion a very economical choice for many jobs, offering an attractive balance in between cost and performance.
Beneficial Manufacturing Speeds
While maintaining the cost-effectiveness of the products, one more notable advantage of plastic extrusion hinges on its rapid production rates. This efficiency in the production process is attributed to the constant nature of the extrusion process, enabling high-volume production in a reasonably short time period. The speed of manufacturing directly associates to a decrease in labor costs and an increase in result, consequently enhancing the overall financial stability of the procedure. In addition, the hectic manufacturing does not jeopardize the quality of the end product, guaranteeing trustworthy and consistent outcomes. This mix of rate, high quality, and cost-effectiveness emphasizes the substantial financial advantage of carrying out plastic extrusion in different tasks.
Versatility and Personalization: The Staminas of Plastic Extrusion
Among the noticeable toughness of plastic extrusion depends on its versatility and customization capacity. These qualities unlock to unrestricted design possibilities, offering manufacturers the capacity to tailor products to specific requirements. This enhanced degree of customization not just boosts item performance yet additionally dramatically improves product individuality.
Endless Layout Opportunities
Plastic extrusion beams in its capacity to offer almost limitless style opportunities. This technique offers flexibility to create complicated shapes and intricate accounts, an accomplishment tough to attain with other manufacture strategies. Owing to the fluid nature of liquified plastic, the process is flexible enough to produce a varied moved here variety of kinds, measurements, and sizes. The plastic can be manipulated to match one-of-a-kind specs, find out here allowing for the manufacturing of customized geometries and meeting particular client needs. Plastic extrusion can deal with a range of plastic types, broadening its application scope. This versatile strategy, as a result, serves a vast array of sectors from construction to automobile, packaging to electronic devices, and past. With plastic extrusion, the design opportunities are basically endless.
Improving Item Individuality
The versatility of plastic extrusion can considerably boost product uniqueness. This procedure allows designers to trying out different forms, dimensions, and colors, providing the liberty to produce distinct items that stand out in the market. It is this customization that offers a distinct identity to each item, identifying it from its rivals.
Along with its aesthetic advantages, the customizability of plastic extrusion additionally uses functional benefits. Developers can change the homes of the plastic according to the details requirements of the application, enhancing the product's performance. They can make the plastic a lot more flexible, a lot more durable, or much more immune to warm, depending on what the product needs. Hence, plastic extrusion not only boosts product individuality but also its energy and marketability.
Layout Limitations in Plastic Extrusion: What You Need to Know
Exactly how can develop restrictions possibly influence the procedure of plastic extrusion? While plastic extrusion is flexible, design restrictions can stop its advantages. Comprehending these restrictions is important for efficient implementation of plastic extrusion in your jobs.
Reviewing the Ecological Impact of Plastic Extrusion
While understanding layout constraints is a considerable aspect of plastic extrusion, it is similarly essential to consider its ecological ramifications. The procedure of plastic extrusion includes melting plastic products, possibly launching damaging gases right into the atmosphere. Additionally, the resulting items are typically non-biodegradable, adding to landfill waste. Advancements in innovation have actually enabled for even more environmentally-friendly techniques. For example, utilizing recycled plastic materials in the extrusion procedure can reduce ecological effect. Additionally, creating biodegradable plastic choices can assist reduce waste concerns. Reviewing these environmental elements is essential when carrying out plastic extrusion projects, making certain an equilibrium between performance, cost-effectiveness, and environmental obligation.
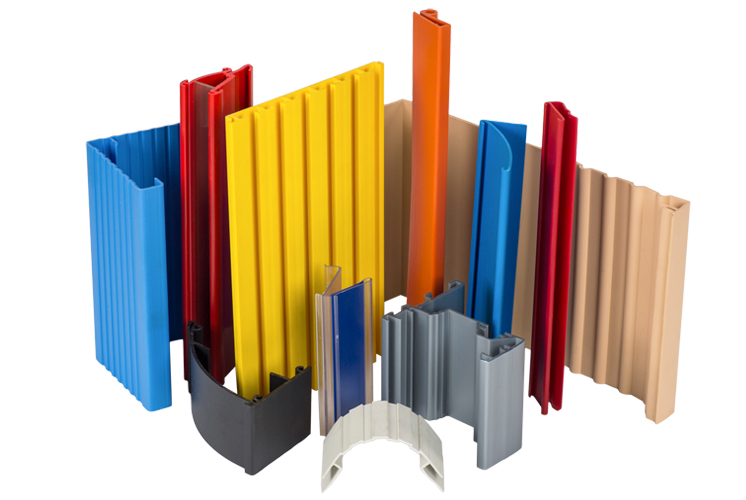
Case Research: Effective Projects Utilizing Plastic Extrusion
Success stories in the field of plastic extrusion are plentiful, showing both the adaptability and effectiveness of this production process. One notable instance is the development of PVC pipes utilized in modern-day plumbing. This process entails melting plastic and developing it right into a continuous tube, supplying considerable cost and longevity advantages. One more successful instance is the production of plastic movie for product packaging and farming. With extrusion, producers can produce highly personalized, slim, and durable films. Automotive sectors additionally look at more info benefit, utilizing extruded plastic for components like trim or seals, enhancing lorry longevity. These circumstances show plastic extrusion's critical role in different fields, vouching for its adaptability, cost-effectiveness, and trusted output.
Final thought
In final thought, plastic extrusion uses a efficient and affordable approach for producing intricate shapes with marginal waste. Incorporating plastic extrusion right into jobs can lead to successful outcomes, as shown by many case research studies.
Plastic extrusion, a staple in the production sector, is a procedure that includes melting raw plastic product and improving it into a continuous profile. Plastic extrusion can handle a variety of plastic types, broadening its application extent.Just how can design limitations possibly influence the process of plastic extrusion? The procedure of plastic extrusion includes melting plastic materials, possibly launching dangerous gases into the setting. Using recycled plastic products in the extrusion process can lower environmental effect.
Report this page